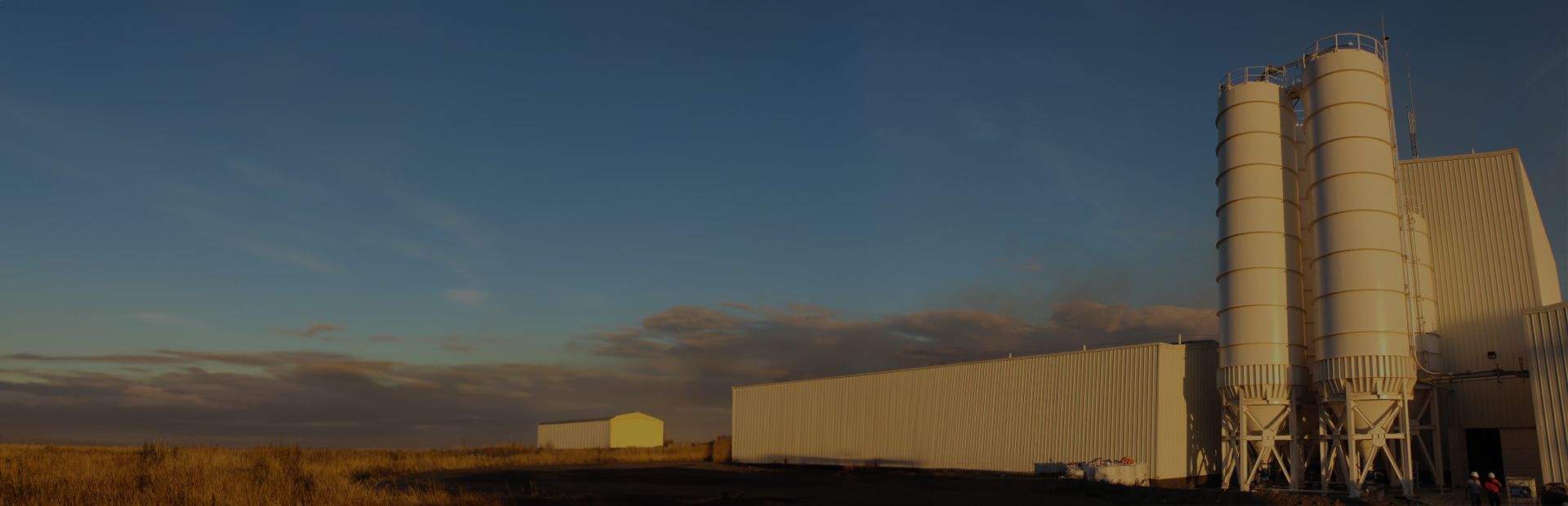
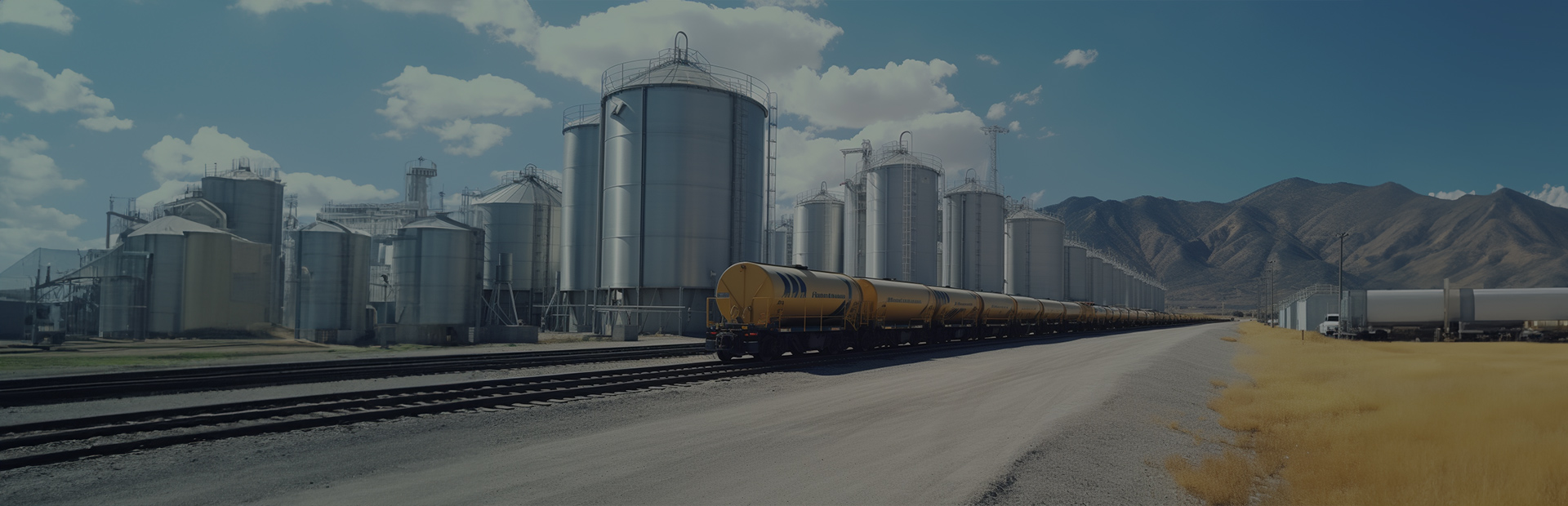
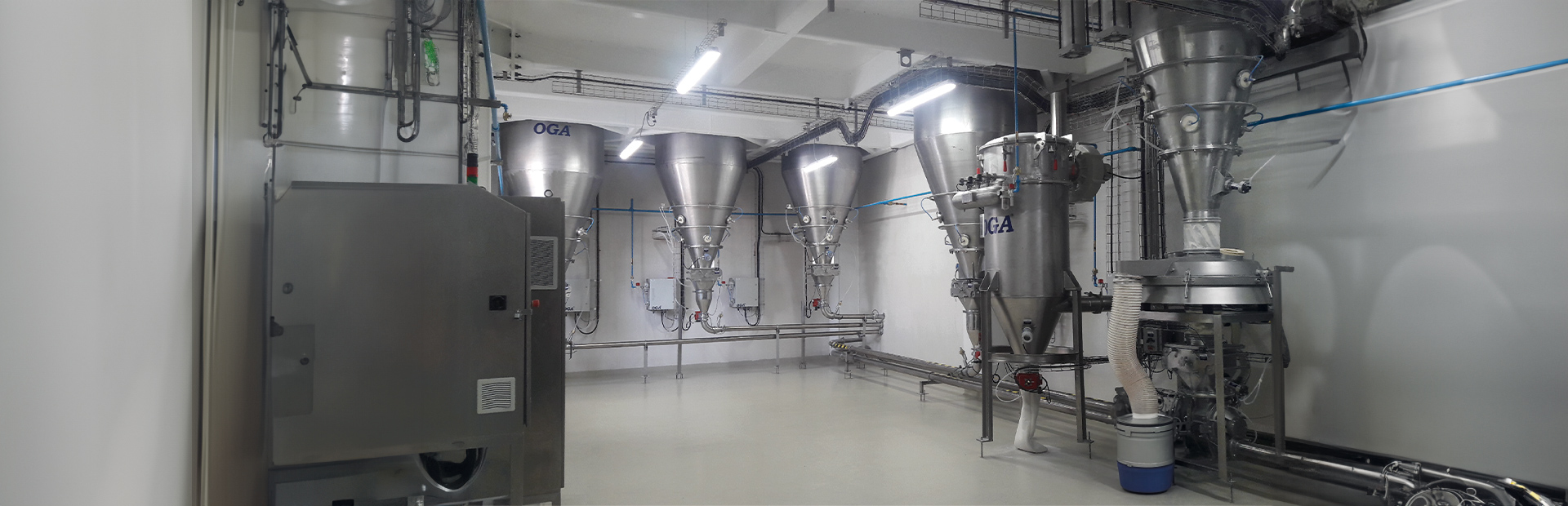
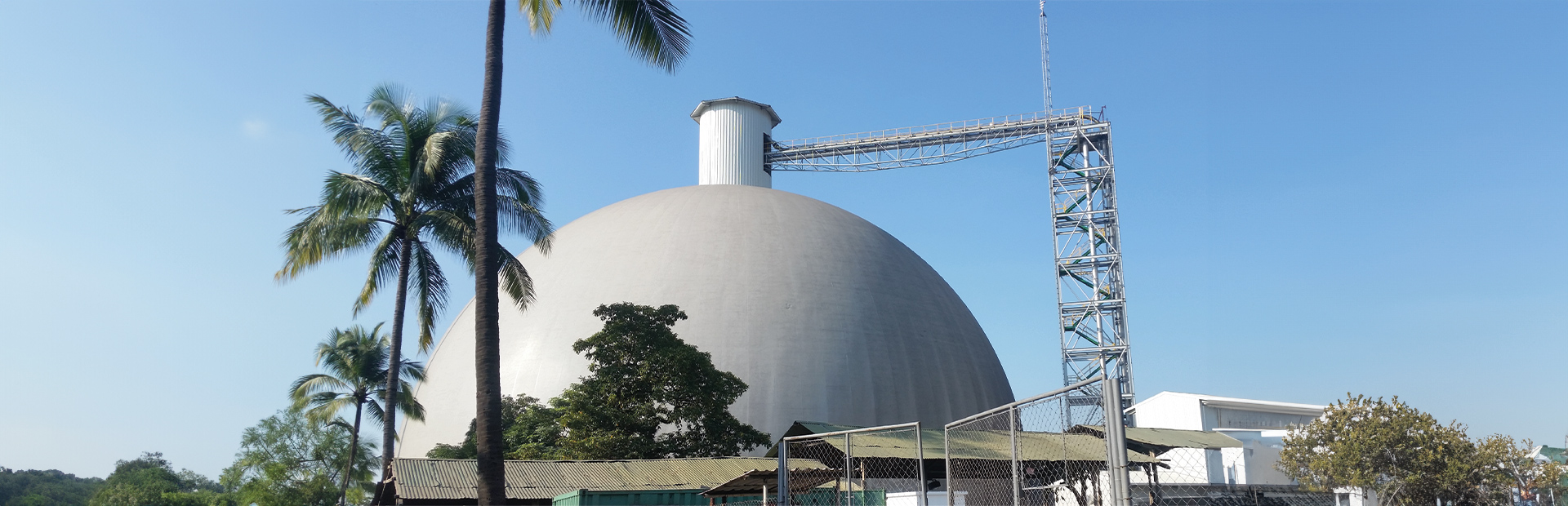
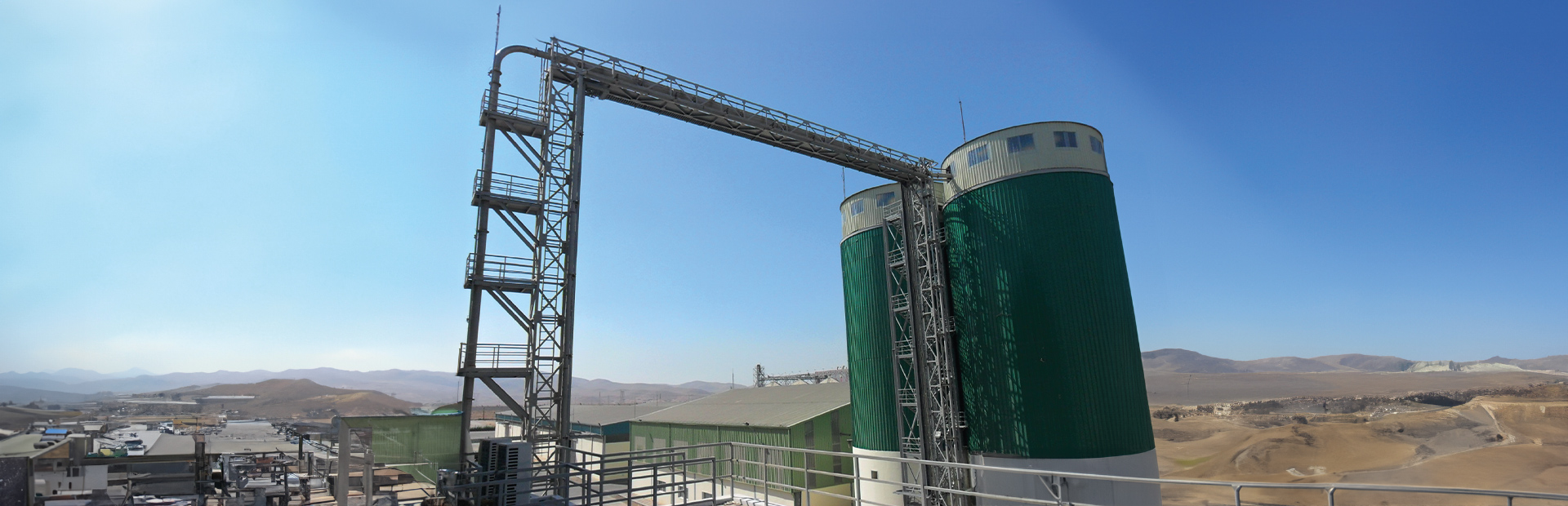
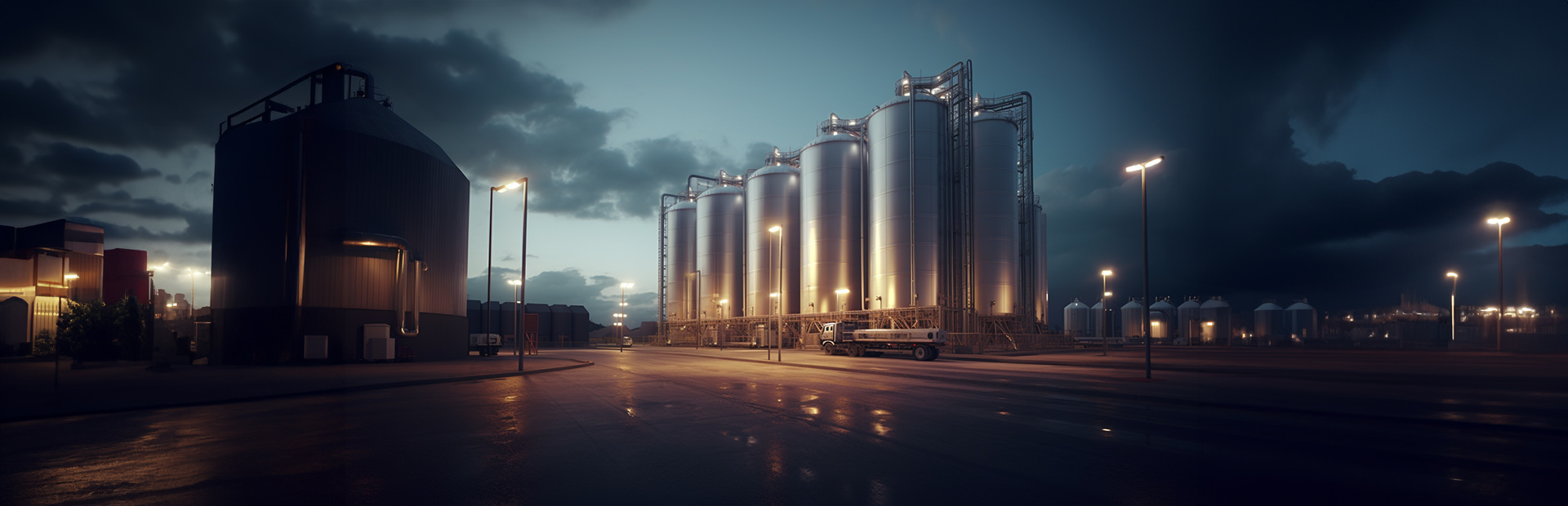
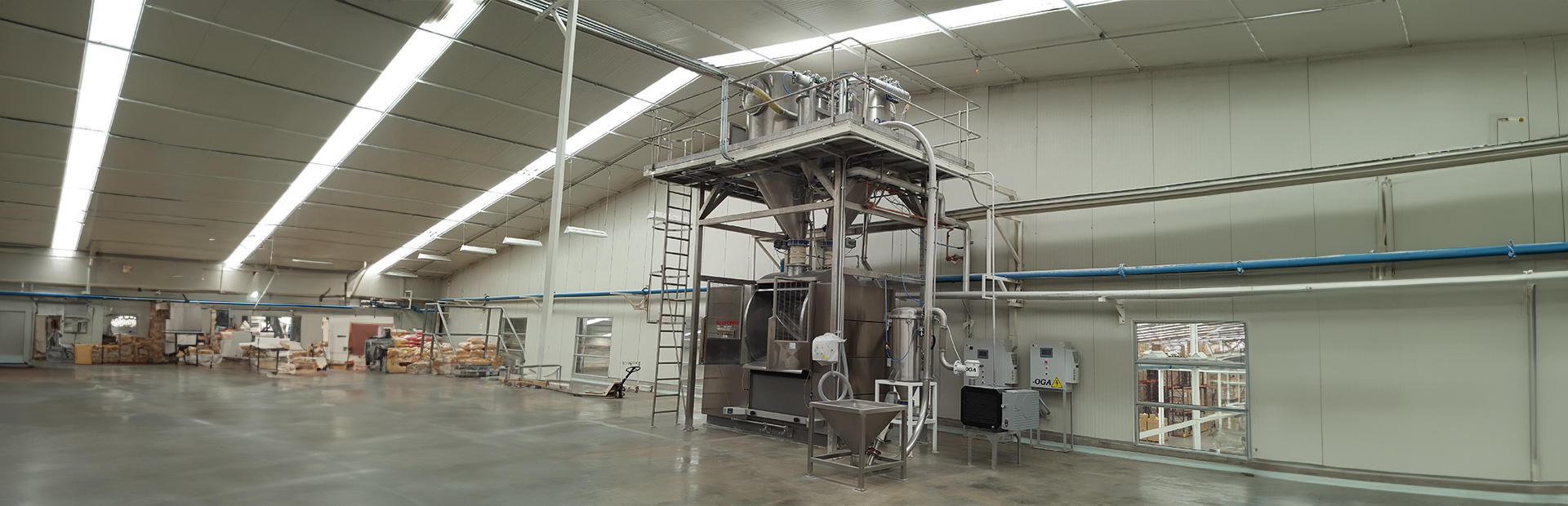
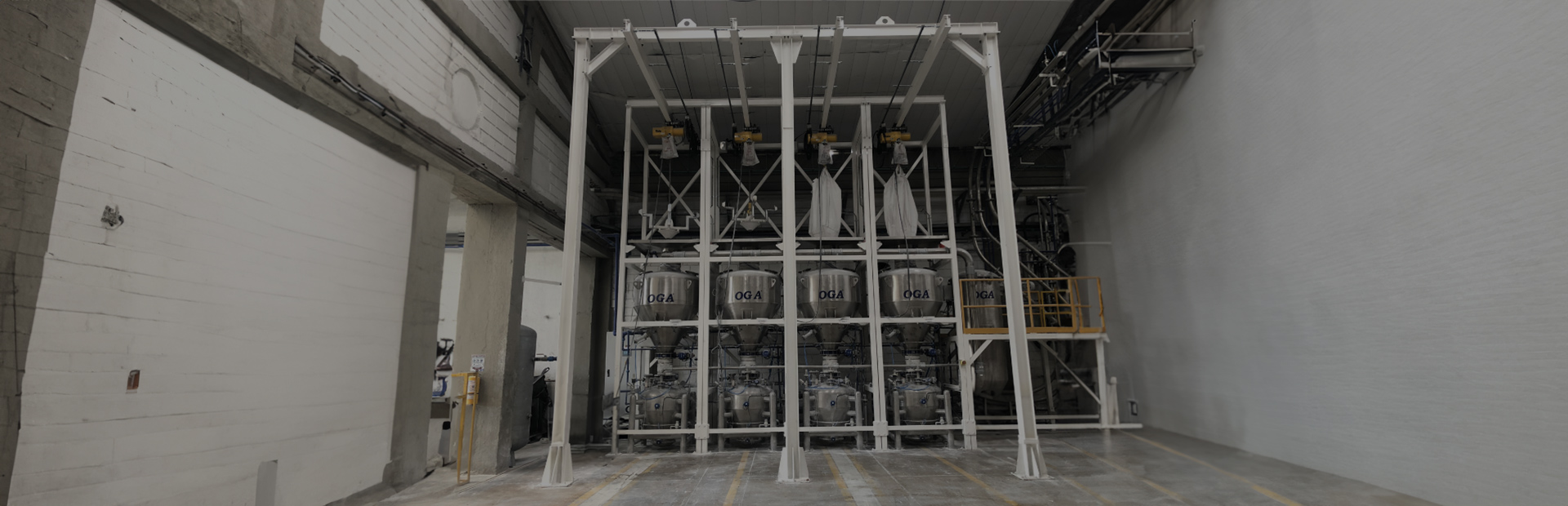
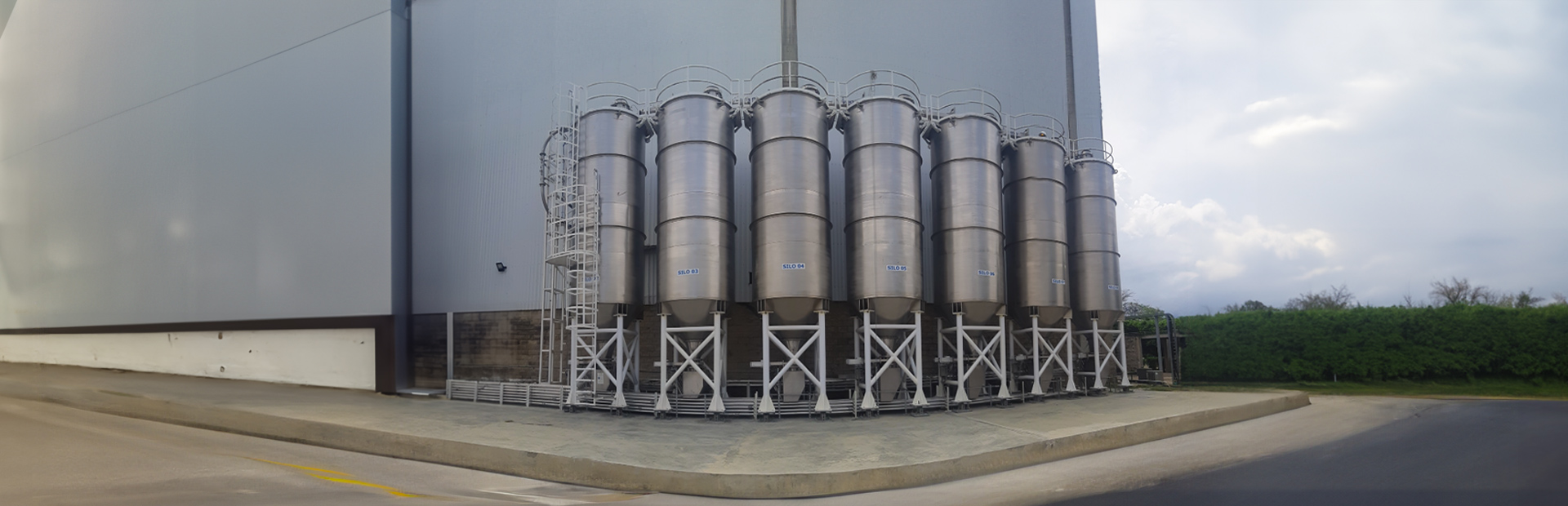
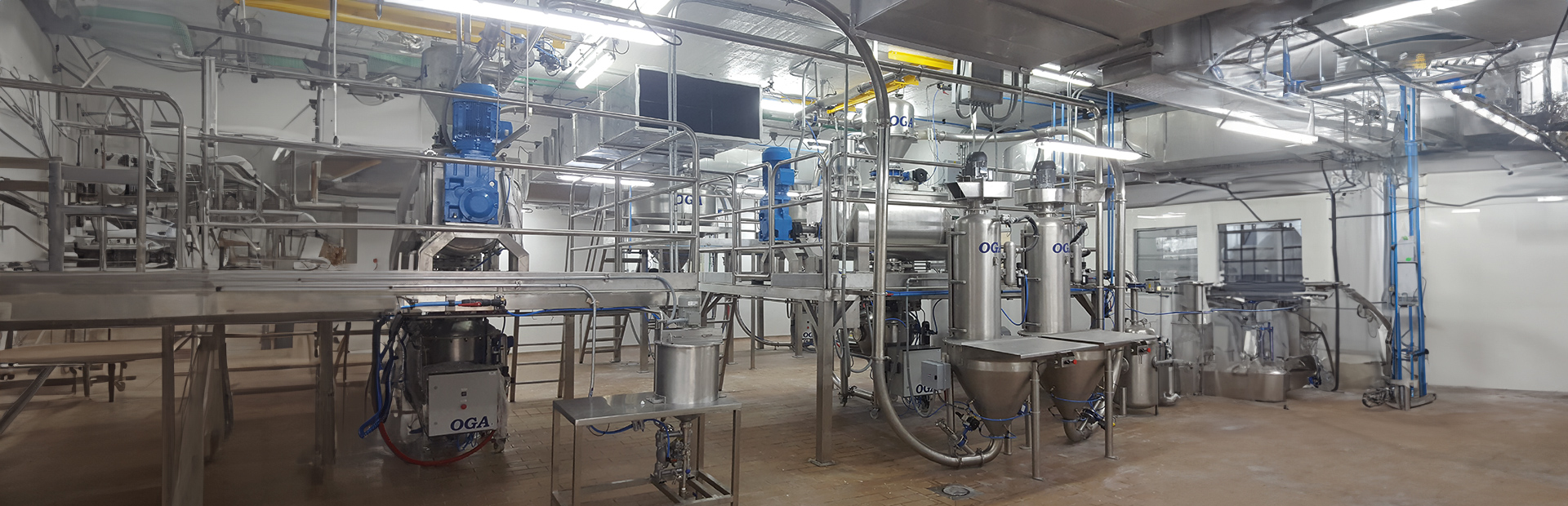
Design and manufacturing of tailor-made systems for your industry, with global coverage.
Design and manufacturing of tailor-made systems for your industry, with global coverage.
Design and manufacturing of tailor-made systems for your industry, with global coverage.
Design and manufacturing of tailor-made systems for your industry, with global coverage.
Design and manufacturing of tailor-made systems for your industry, with global coverage.
Design and manufacturing of tailor-made systems for your industry, with global coverage.
Design and manufacturing of tailor-made systems for your industry, with global coverage.
Design and manufacturing of tailor-made systems for your industry, with global coverage.
Design and manufacturing of pneumatic transport systems applied to multiple industries.
Design and manufacturing of pneumatic transport systems applied to multiple industries.
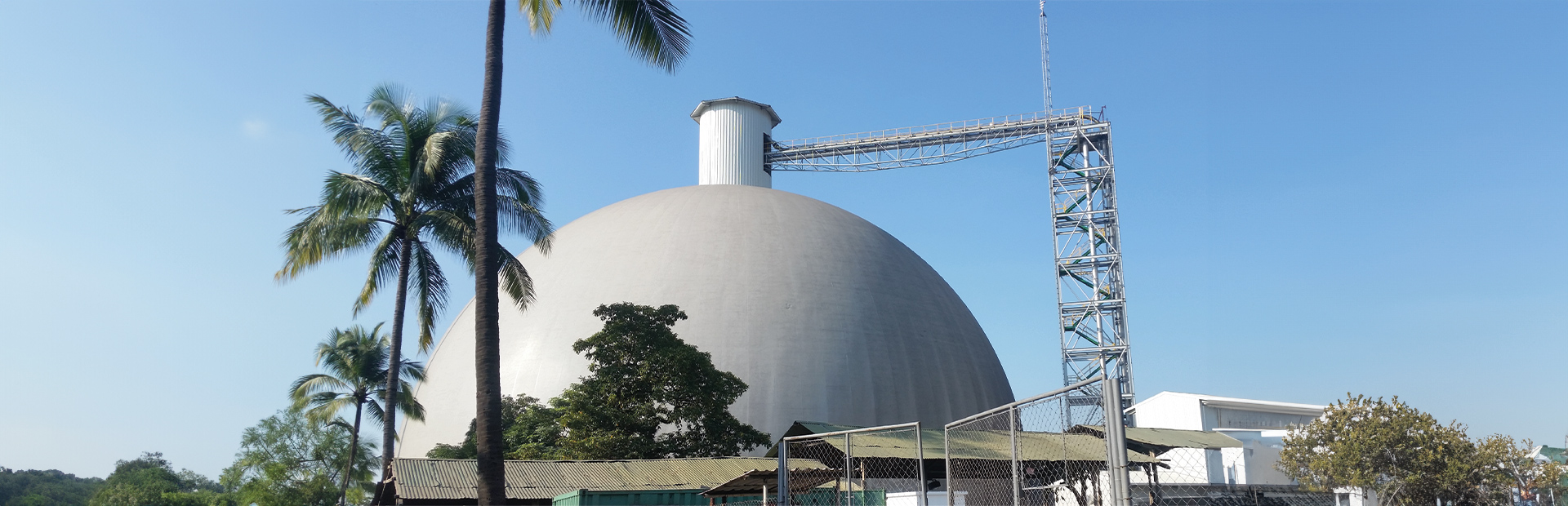
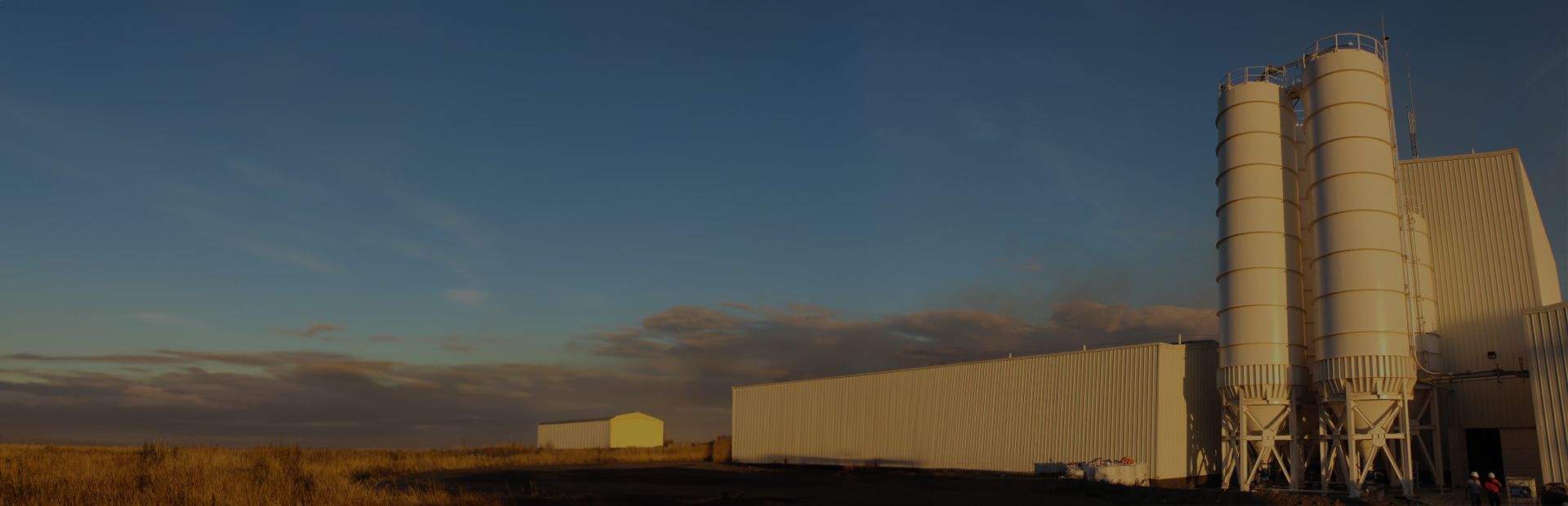
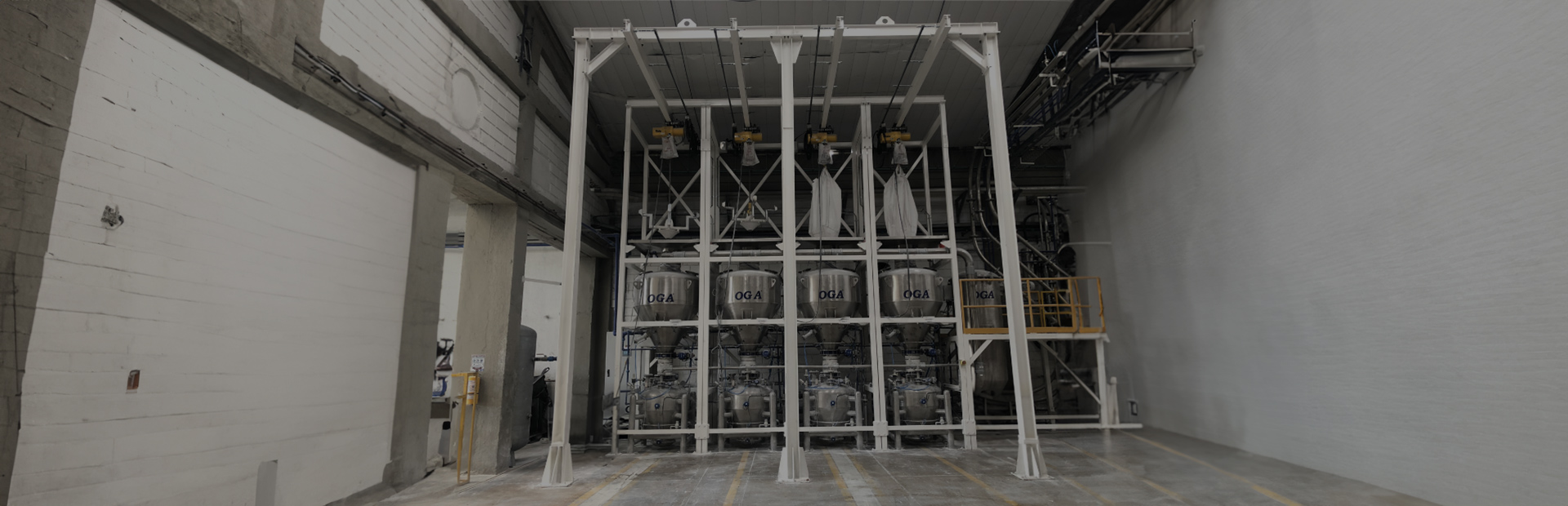
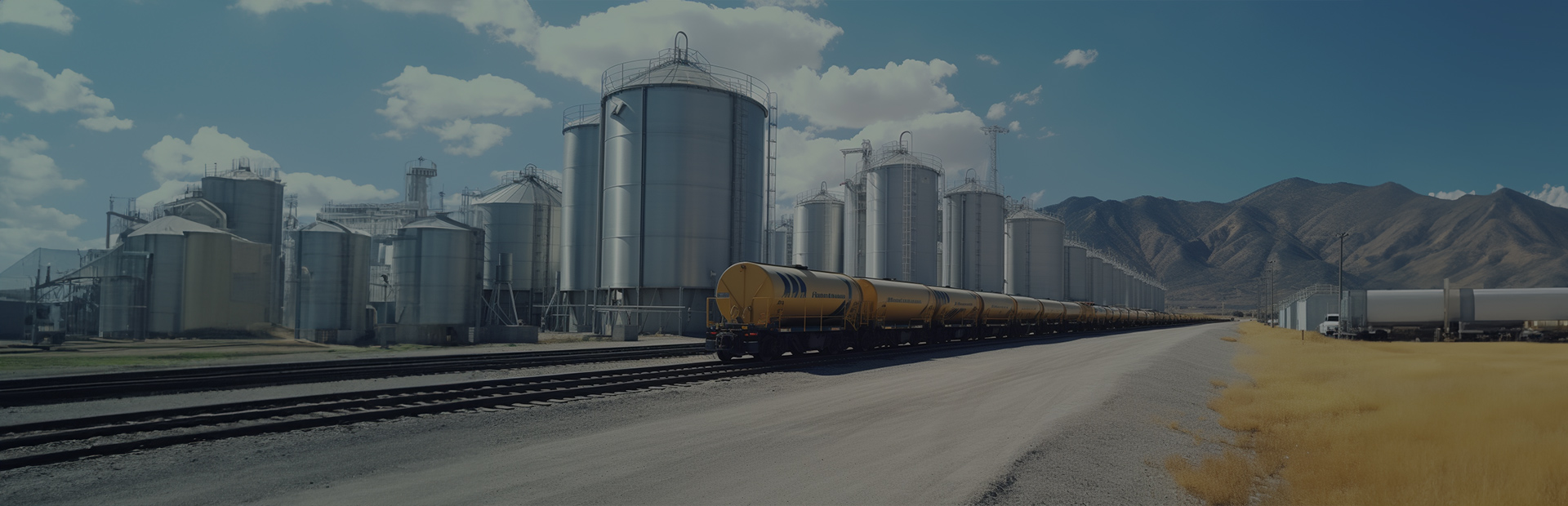
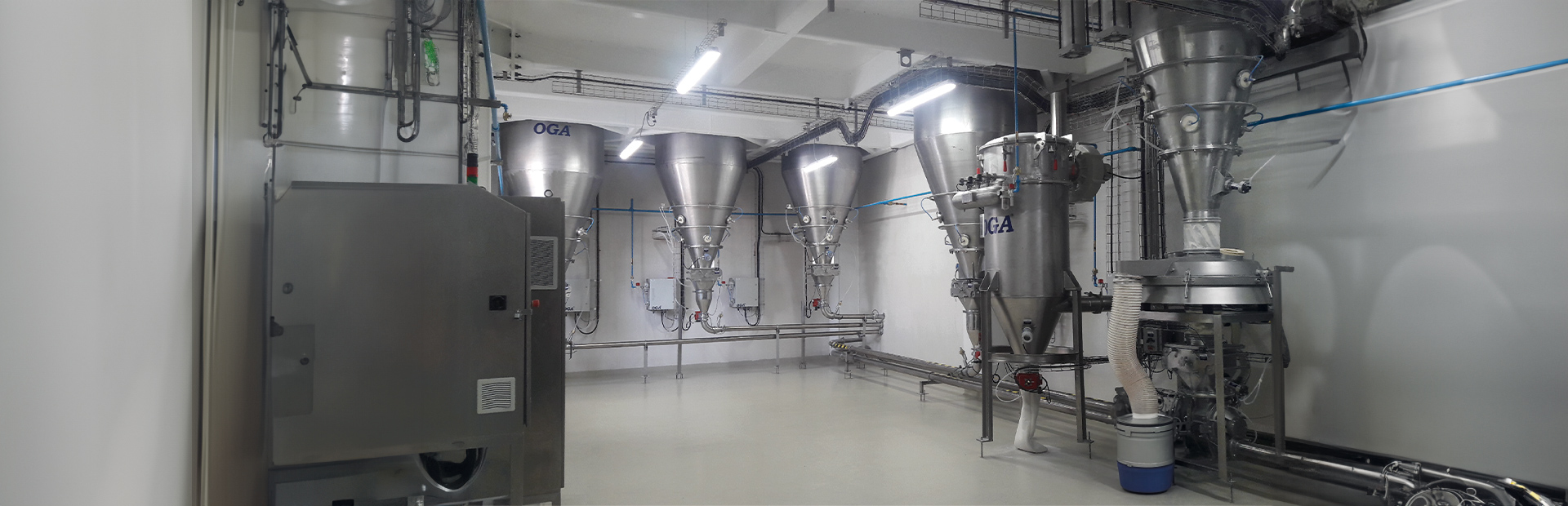
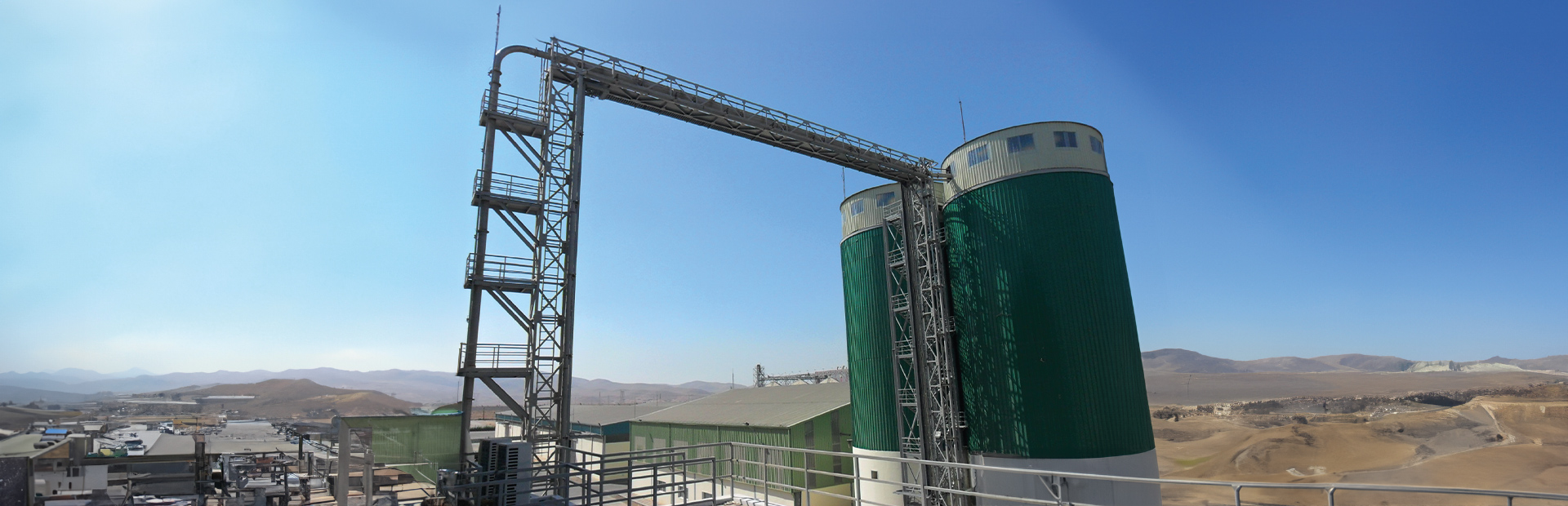
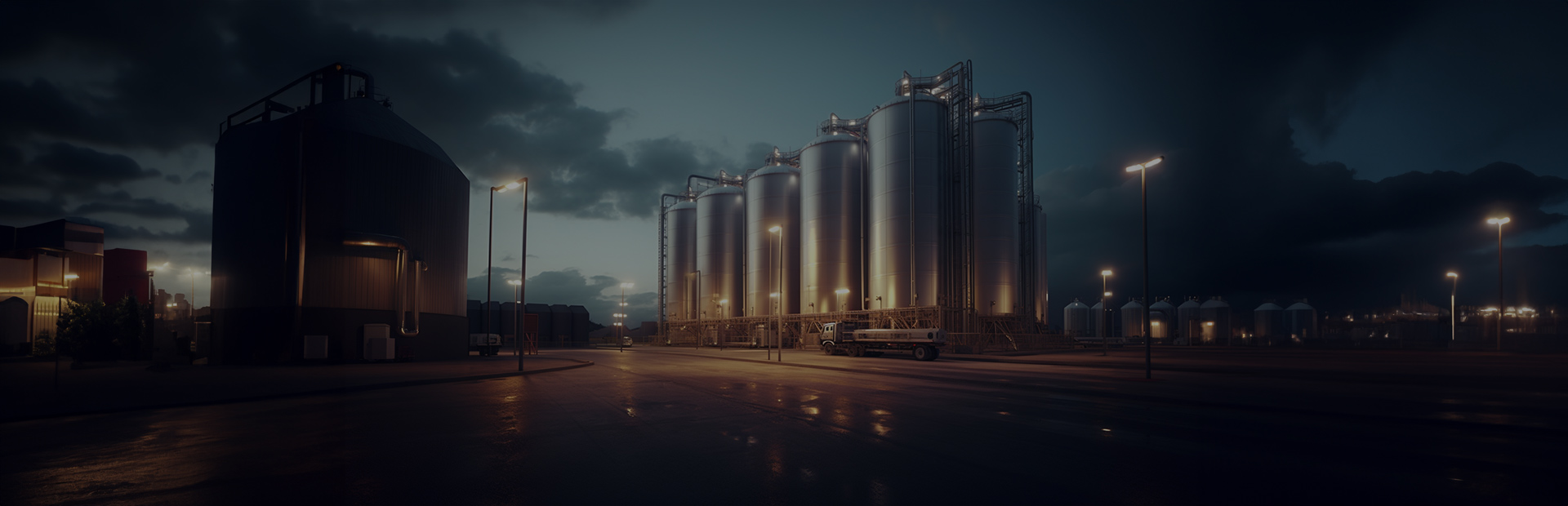
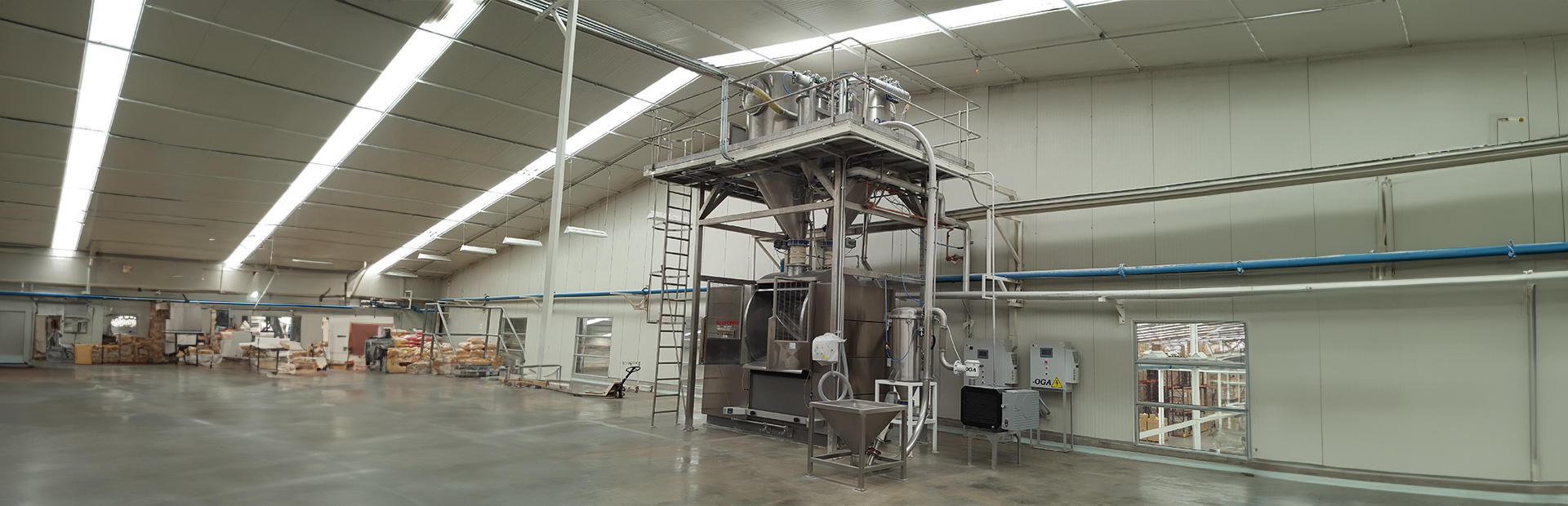
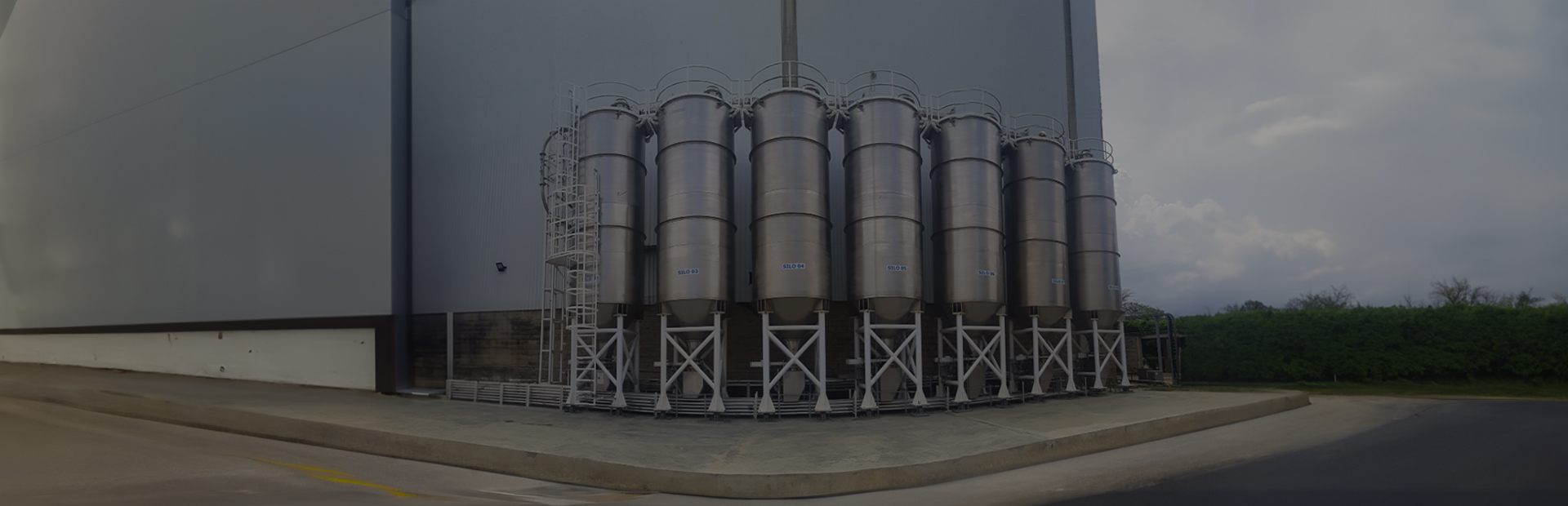
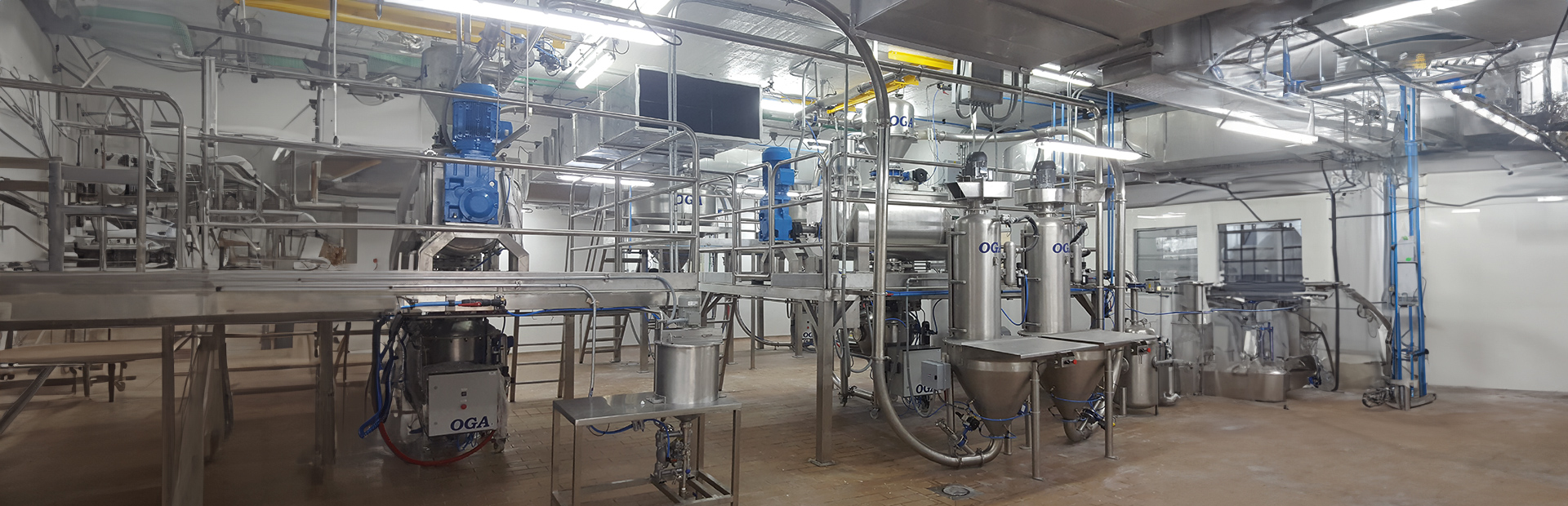
Design and manufacturing of pneumatic transport systems applied to multiple industries.
Design and manufacturing of pneumatic transport systems applied to multiple industries.
Design and manufacturing of pneumatic transport systems applied to multiple industries.
Design and manufacturing of pneumatic transport systems applied to multiple industries.
Design and manufacturing of pneumatic transport systems applied to multiple industries.
Design and manufacturing of pneumatic transport systems applied to multiple industries.
Design and manufacturing of pneumatic transport systems applied to multiple industries.
Design and manufacturing of pneumatic transport systems applied to multiple industries.
Design and manufacturing of pneumatic transport systems applied to multiple industries.
Design and manufacturing of pneumatic transport systems applied to multiple industries.

Sugar Mills
For several decades, OGA has been dedicated to the study and refinement of PNEUMATIC TRANSPORT SYSTEMS for handling SUGAR, primarily in sugar mills. In this process, the success factors in multiple installations have been analyzed and determined, achieving total effectiveness in the systems implemented in SUGAR MILLS worldwide. OGA has managed to control the more than 27 variables that make up the design of a PNEUMATIC TRANSPORT SYSTEM IN SUGAR INDUSTRIES to handle the speeds and concentrations of the product accurately along the transport pipeline. Thus, after multiple field verifications with the system in real operation over actual distances, we have control and management of the most important variables in the final product (AM and CV).
The pursuit of the best production processes globally has led to increasingly stringent regulations regarding the manufacturing plants of food products, always seeking the protection of the end consumer. Based on this, health authorities are demanding cleaner production and material handling processes. Additionally, OGA has designed pneumatic transport systems for closed-loop handling, replacing conventional transport mechanisms. The implementation of OGA PNEUMATIC TRANSPORT SYSTEMS in sugar mills contributes to their compliance with global regulations regarding GMP, HACCP, ISO, FSSC 22,000.
Impact of Velocity on Transported Product
One of the major concerns in the sugar industry when evaluating the implementation of pneumatic transport systems is the potential risk of product deterioration. This concern is well-founded, as incorrect handling of variables in a pneumatic transport system for this industry can have a significant negative impact on product variables such as CV and AM. In conclusion, this concern has been the main focus of study and development for OGA equipment. Throughout this process, we have meticulously delved into all the variables involved in this handling to ensure that today we can confidently offer systems that do not affect the most important physical characteristics of the product.



Benefits of OGA Pneumatic Transport Systems.
Sugar Industries
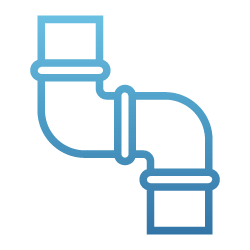
Route Flexibility:
A significant difference between conventional conveyors and OGA systems is that all traditional equipment can only handle a single flow direction, either vertical or horizontal. Our systems can take the product from one point of origin and transport it throughout the entire production plant using a single system, combining vertical and horizontal paths interchangeably thanks to the use of a single pipeline equipped with long-radius bends to adapt to any process.
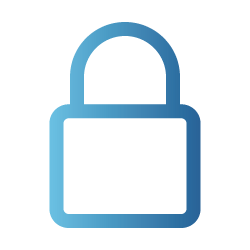
Transport Hermeticity:
This is one of the main reasons why our clients opt for the implementation of an OGA system in pursuit of compliance with HASS, BPM, and FSSC 22.000 standards. OGA transport systems handle the product within a 100% closed pathway, preventing product contamination from external agents and the pollution of the production environment with the finished product.
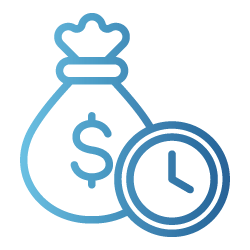
Low maintenance cost:
Due to the fact that OGA pneumatic transport systems use gas to move the product, the mechanical or moving parts are minimal, resulting in a high degree of reliability and stability in our equipment. This leads to a significantly reduced maintenance cost in the systems.
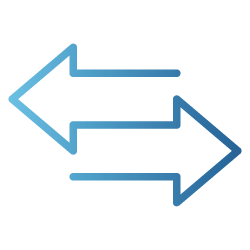
Multiple destination routes:
In OGA pneumatic transport systems, there is a single transport pipeline that allows the implementation of route branches, reaching different and distant destination points throughout the entire plant. Once a base system is implemented, additional branch routes can be expanded without affecting the initially installed system.
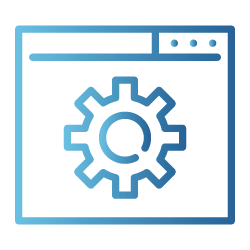
Control system software:
OGA systems come with a control system that can be integrated into the plant’s general software to interact automatically with the entire factory. Alongside this process, variables can be graphed, process traceability can be established, hierarchy levels can be determined for control, automatic maintenance tasks can be performed, remote monitoring via the internet can be facilitated, weight reporting can be conducted, and integration with other process equipment can be achieved.
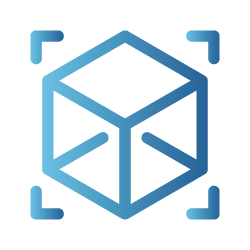
Customized Design:
In OGA pneumatic transport systems, there is a single transport pipeline that allows the implementation of route branches, reaching different and distant destination points throughout the entire facility.
Furthermore, once a base system is implemented, additional branch routes can be expanded without affecting the initially installed system.
Typical Applications in Sugar Industries
The primary application of OGA PNEUMATIC TRANSPORT SYSTEMS lies in handling finished products, typically from the discharge of dryers to storage silos and/or conditioning, followed by transportation to packaging lines. With the use of our systems, the final product is entirely shielded to prevent deterioration and/or contamination. Although the handling of systems through dense phase is usually in batches, OGA has developed Z2 series systems, wherein material intake and discharge occur continuously, achieving distances exceeding 200m and flow rates above 100 tons per hour.
All OGA PNEUMATIC TRANSPORT SYSTEMS feature a sequence of air pressure filters that sequentially remove moisture, particles, oil, and odors from the compressed air, achieving retentions as fine as 0.001 microns.
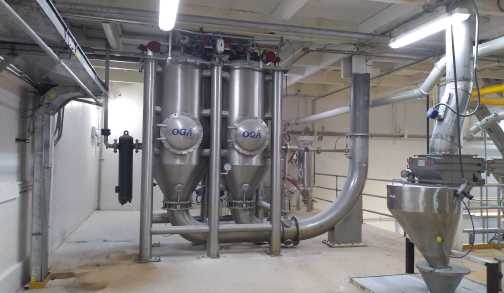
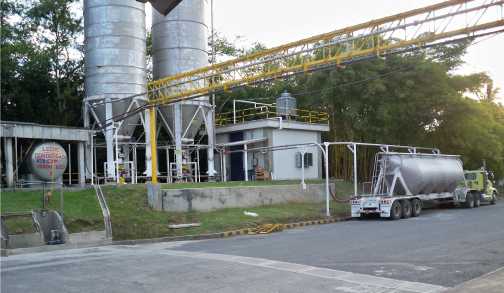
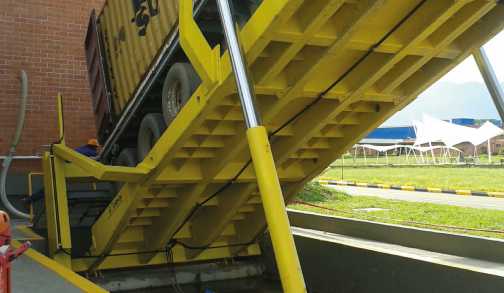
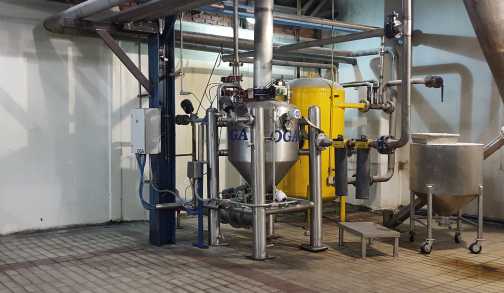
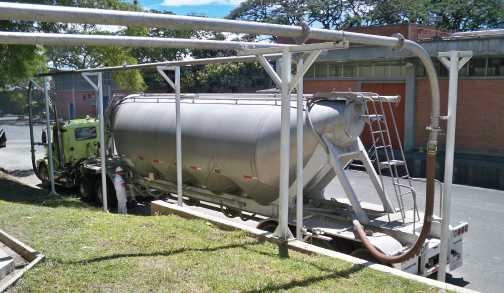
Complementary Systems
Complementary Systems
- Bulk unloading systems from containers to silos
- Storage silos for powdered or granular products
- Production process control via SCADA software
- Bulk unloading systems from pressurizable hopper cars, trailers, or railways
- Raw material silo weighing systems
- Sieving systems, granulometric selection of raw materials, and final product
- Design of production plants based on solids handling and good manufacturing practices
- Unloading systems from hopper railcars to silos
- Transport systems to daily silos within production plants
- Automated feeding of production processes from storage silos
- Unloading systems from big bags and transport to storage silos
- Supply of Bulk Tipping Platforms
- Inventory Control
- Pneumatic Transport of Delicate Products
- Handling of Big Bags, Sacks, Sheets, and Boxes
- Sugar Dosing
- Product Feeding into Process
- Sieving and Solid Classification